
Strategies To Improve Pallet Rack Safety in The Warehouse
Pallet Rack Safety
Pallet rack damage is a serious workplace health and safety hazard in warehouses. The potential of forklift collisions or accidents due to poorly loaded pallets is a big worry in a busy warehouse setting. We've developed a list of techniques to improve pallet racking safety in your warehouse to safeguard the safety of your employees and merchandise.
Implementing correct safety precautions and performing routine maintenance can reduce the chance of employee injury as well as product damage.
Here are some ideas for making your warehouse's pallet racking safer.:
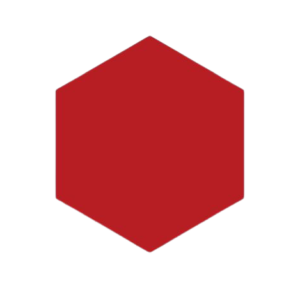
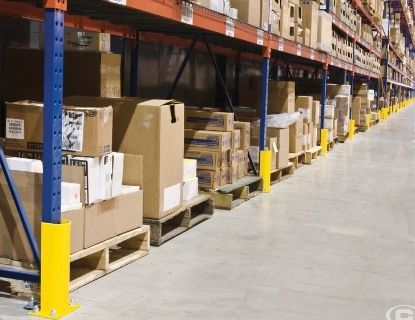
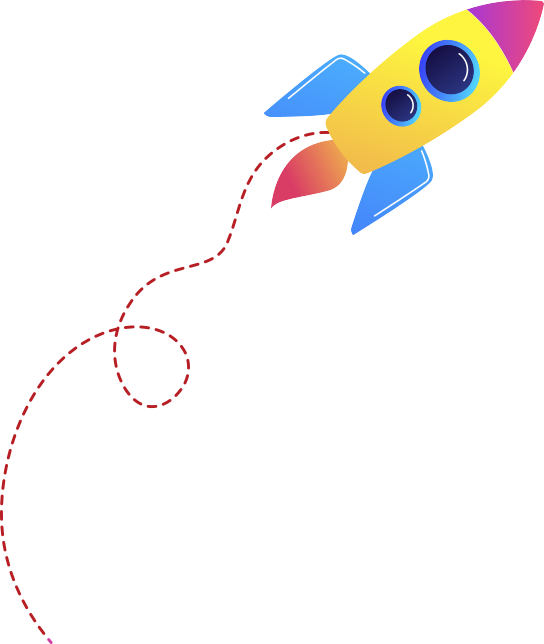
Warehouse's Pallet Racking Safer
START WITH REGULAR INSPECTIONS
PLACE THE LOAD IN A SQUARE POSITION
NEVER EXCEED THE RACK CAPACITY
KEEP THE AISLES CLEAR
TRACK AND REPORT
Start With Regular Inspections
The examination is the only method to find out where you stand. Either your skilled workers or a third party performs it. Inspections must be conducted on a regular basis and must include a tour of the facility and close observation of the racking. Impact sensors on forklifts or directly on the rack can't always detect damage caused by pallets rubbing against columns and bracing, nor can they always detect loosened safety bars and safety pins. There's no other method to determine whether or not your racks are compatible.
Place The Load In A Square Position
Ensure that your forklift operators are appropriately trained to place pallets on rack beams. This entails arranging the pallets in a square and even pattern, with the front and back of the pallets partially covered.
Never Exceed The Rack Capacity
Despite the fact that load capacity is emphasised as a safety measure, exceeding rack capacity is nevertheless a typical occurrence in warehouses. Ensure that all personnel has access to load capacity documentation and signage and that all staff is taught to comprehend the beam capacity of each rack. Allowable safe limits are in place for a purpose; employees should follow them for their personal safety, as well as the protection of others, warehouse equipment, and products.
Keep The Aisles Clear
If safety measures are not adopted and enforced, operating forklifts can be a very dangerous job. For ease of access, aisles must be kept clean, as any obstacle could result in catastrophic injury or damage to warehouse equipment or merchandise. Aisle obstructions are a certain way to cause forklift collisions in your warehouse. If you care about the safety of your employees, warehouse equipment, and products, you'll make sure that these precautions are not merely taught and posted, but also enforced and inspected.
Track And Report
Finally, because racking safety is a continuous process, we want to report and retain a written history of what is going on with the racking so that the process can be held accountable. Tracking and reporting concerns ensure clear communication throughout the chain of command, ensuring that everyone is aware of what is going on. This, in turn, leads to accountability for the flaws that have been identified. Everyone is informed, and things should get done, thanks to a clear accountability process. In addition, tracking and reporting will help you create a timeline.